ACTIVE CHILLED BEAMS
In a chilled beam, the term “induction” is used to describe the process of injecting primary air under pressure through a nozzle, which in turn entrains return or plenum air at the discharge of the nozzle.
The amount of air that is entrained (Q induced) vs. the amount of air injected (Q injected) is referred to as the induction ratio.
The induced air is drawn through a water coil that may either heat or cool the air before it comes in contact with the injected air discharging from the nozzle. The amount of energy transferred by the water coil is influenced by several factors, including the induced air temperature, water supply temperature, volume of induced air moving through the water coil, and amount of coil surface area.
Figure 1: Process of injecting primary air under pressure through a nozzle
When designing a chilled beam system, one parameter that is often used is the transfer efficiency. This is the fraction of heating or cooling energy that is provided by the water coil heat transfer (q coil) vs. the volume of primary air (Q primary air).

The transfer efficiency is related to the overall HVAC system efficiency. It takes less brake horsepower to move thermal energy with water than it does with air, as the volume of air needed is significantly larger due to the lower amount of thermal energy it can store. Several recent building designs have indicated a potential brake horsepower reduction of 10 to 15%. The potential saving is higher, but limited by the system choices made by the designer, as well as the primary air volume requirements. To minimize the energy spent moving air, the primary air volume would be no more than the requirements for fresh air.
Knowing the induction ratio for chilled beams can be beneficial when designing the building’s HVAC system. For example, when selecting active chilled beams for use in a patient room, ASHRAE Standard 170 calls for a minimum of six air changes, with a minimum of two air changes being fresh air. All six air changes can be fresh air, but more energy efficient designs will typically have the fresh air being limited to the minimum two changes. This means the designer needs to select an induction ratio of 2 cfm induced to 1 cfm primary air to meet the required six room air changes.
Induction ratio for an active chilled beam is typically determined by calculating an energy balance on the beam. Basically, the total energy transferred by the water to the induced air is used to determine the volume of induced air. Determining the induction ratio is most often accomplished using air temperature measurements. Once we know the primary air temperature, induced air temperature, and discharge (mixed) air temperature, the induction ratio can be calculated. Discharge air temperature is influenced by the number and location of primary air nozzles along the length of the discharge slot, and should be determined in a laboratory setting, not the field. This will ensure that a true average discharge air temperature is recorded.
DIFFUSERS
Unlike an active chilled beam, the induction ratio of a ceiling diffuser is not determined by the volume of air entering an opening, but rather the volume of air entrained along the discharge path of the diffuser (Figure 2). As supply air is moving from the outlet, the air velocity slows down due to the entrained air mass being added to the moving air. In order to determine the volume of induced air, the distance from the diffuser must be fixed, as the further away from the diffuser the larger the volume of entrained air and the larger the induction ratio. Once a distance is fixed, the entrained air volume can be estimated using the supply air temperature, entrained (room) air temperature, and mixed air temperature (at fixed point).
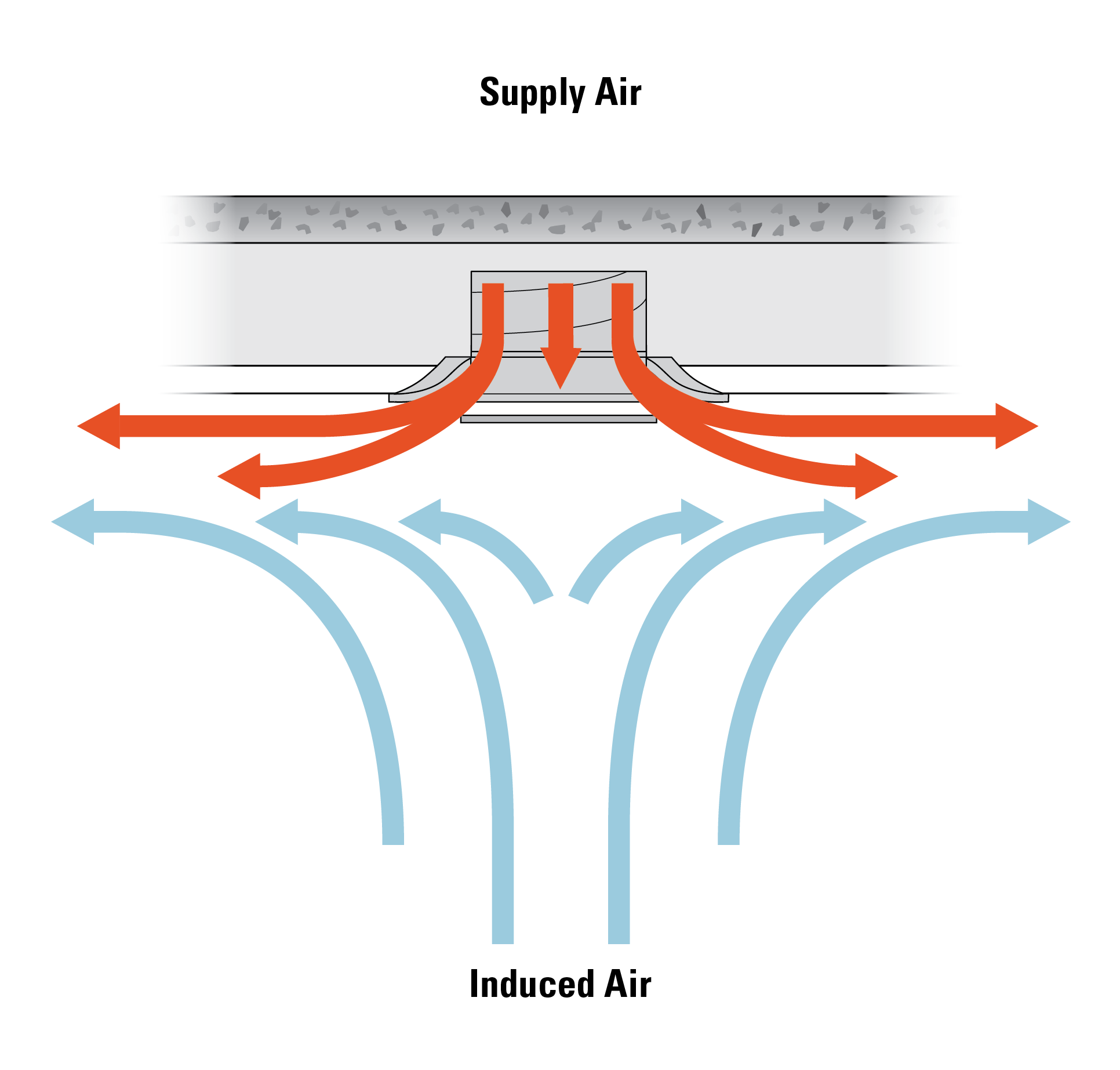
Figure 2: Volume air entrained along the discharge path of diffuser
The mixed air temperature is not an easily determined value, as there can be significant variations in the moving air layer. This layer is often less than ½ inch thick near the discharge, but depending on the type of diffuser, may be much thicker further away. In some cases, the layer may even have detached from the ceiling. The better induction ratios are for diffusers with thin, well-defined discharge patterns with moderate to high discharge velocities.
A better metric to judge the effectiveness of a ceiling diffuser would be the Air Diffusion Performance Index (ADPI). The ADPI is a single number rating index for a diffuser with specified supply air volume, supply air temperature, and space cooling load. It is based on the air speed and effective draft temperature of the occupied zone.
For more information on this and other topics, please see the Price Engineer’s HVAC Handbook, or email beamteam@priceindustries.com or grd@priceindustries.com for specific Beams or GRD questions.